SMAC offer complete sets of equipment for spray painting lines, powder coating lines, electrophoresis lines, anodizing lines, pre-treatment, purification, drying and curing, conveying, and waste gas and wastewater treatment. SMAC's products are widely used in industries such as automotive, motorcycle, bicycle components, IT products, 3C products, home appliances, furniture, cookware, decorative building materials, and construction machinery.
After the workpiece exits the curing oven, it enters the rapid cooling system for cooling treatment.
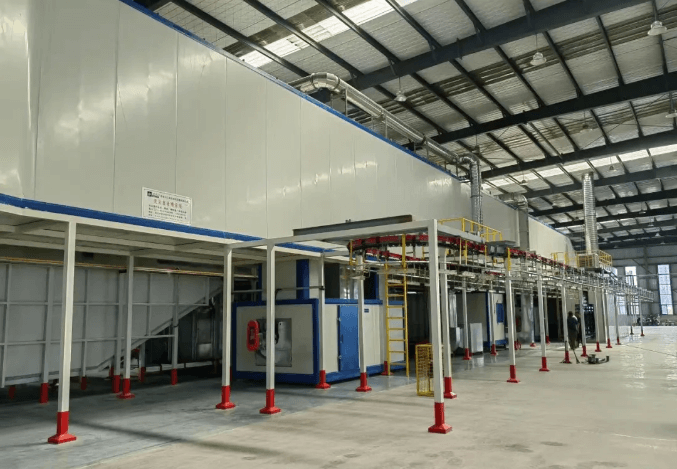
Electrophoretic coating involves applying an external electric field to disperse ionized paint particles suspended in water, allowing them to coat the surface of the workpiece and form a protective layer. This process has several advantages:
Uniform Coating: The coating is applied evenly across the surface.
Strong Adhesion: The paint adheres well to the workpiece.
Minimal Paint Loss: There is little waste of coating material, leading to high utilization rates.
Low Production Costs: The overall cost of production is reduced.
Water-Based Dilution: The paint can be diluted with water, eliminating fire hazards and enhancing safety during production.
These features make electrophoretic coating a popular choice in various industries.
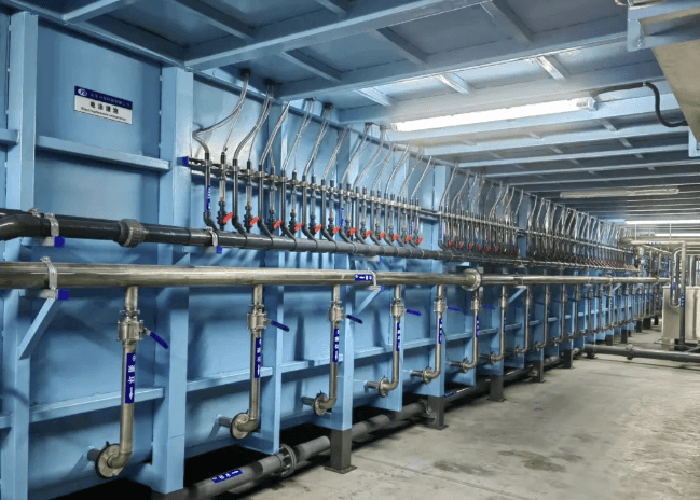
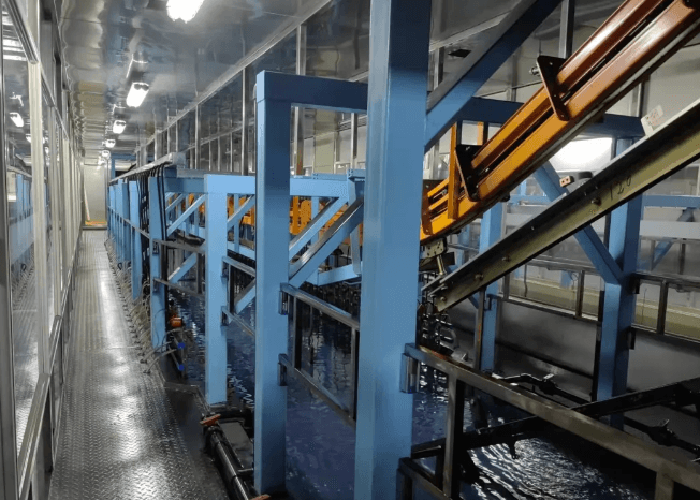
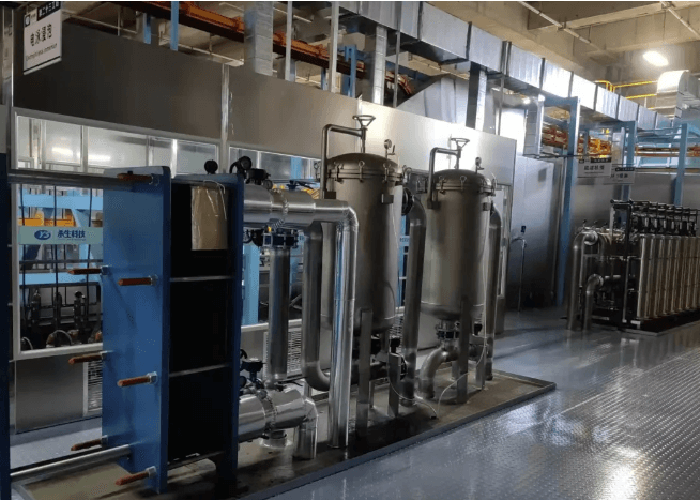
The ultrafiltration (UF) device mainly consists of membrane modules, pumps, piping, and instrumentation, all assembled together. To ensure the normal operation of the ultrafiltration unit, it is typically equipped with filtration and cleaning systems. The primary purpose is to extend the service life of the paint solution, improve the quality of the coating, and ensure the required amount of ultrafiltrate for the normal operation of the equipment.
The ultrafiltration system is designed as a direct circulation system: the electrophoretic paint is delivered through a supply pump to the pre-filter of the ultrafiltration system for 25 μs of pre-treatment. After this, the paint enters the main unit of the ultrafiltration system, where liquid separation occurs via the membrane module. The concentrated paint separated by the ultrafiltration system is returned to the electrophoretic tank through the concentrated paint piping, while the ultrafiltrate is stored in the ultrafiltrate storage tank. The ultrafiltrate in the storage tank is then transferred to the point of use via a transfer pump.
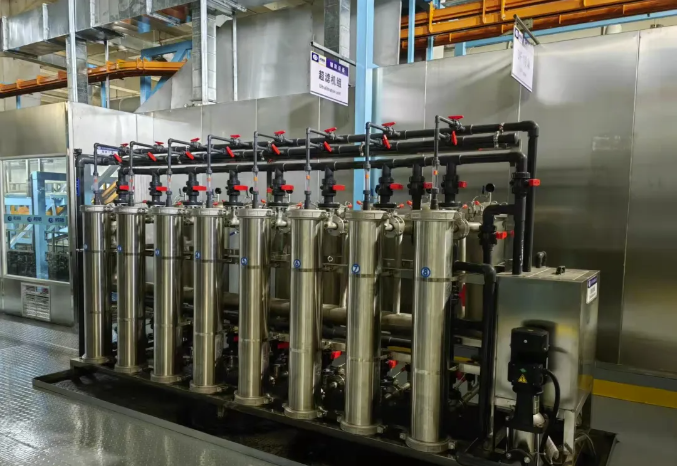
Heating Bag - Baking and Curing
A heating bag is used in the baking and curing process of coatings, particularly in industries such as automotive and manufacturing. Here’s an overview:
1. Function: The heating bag provides controlled heat to the coated workpieces, facilitating the curing of paint or other coatings. This ensures that the coating adheres properly and achieves the desired hardness and durability.
2. Design: Heating bags are typically made from heat-resistant materials and are designed to evenly distribute heat across the surface of the workpieces.
3. Temperature Control: They often come with built-in temperature control systems to maintain the required curing temperatures, ensuring consistent results.
4. Efficiency: Using a heating bag can reduce energy consumption compared to traditional ovens, as it can focus heat directly on the parts being cured.
5. Applications: Commonly used in powder coating processes, electrophoretic painting, and other applications where a durable finish is required.
This method enhances the quality of the finished product while ensuring efficient use of resources.
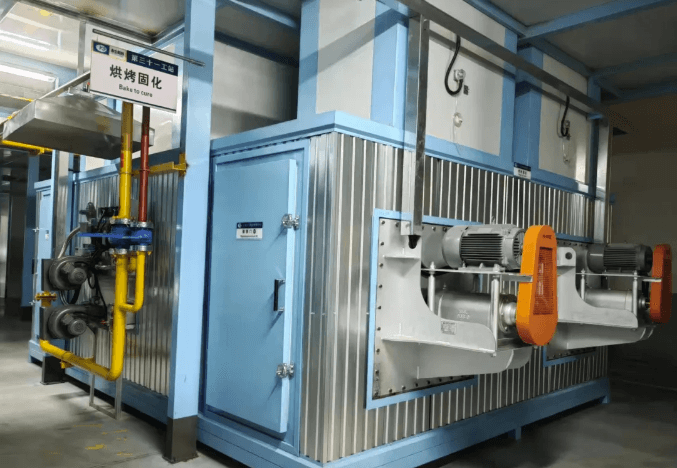
Conveying System
The overhead conveyor system consists of several key components, including a drive mechanism, tensioning device with weights, chains, straight tracks, curved tracks, telescopic tracks, inspection tracks, lubrication systems, supports, load-bearing hangers, electrical control systems, and overload protection devices. Its primary functions are as follows:
1. Operation: When the motor rotates, it drives the tracks through a reducer, which in turn powers the entire overhead conveyor chain. Workpieces are suspended from the conveyor using various types of hangers, facilitating easy handling and operation.
2. Customization: The layout of the conveyor line is determined by the specific working environment and the product process flow, effectively meeting production requirements.
3. Chain Functionality: The chain serves as the traction component of the conveyor. An automatic lubrication system is installed on the chain to ensure that all moving joints receive a precise amount of lubricant.
4. Hangers: The hangers support the chain and bear the load of objects being transported along the tracks. Their design is determined by the shape of the workpieces and specific process requirements. The hooks on the hangers undergo appropriate heat treatment to ensure they withstand prolonged use without cracking or deforming.
This conveying system enhances operational efficiency and reliability in various industrial applications.
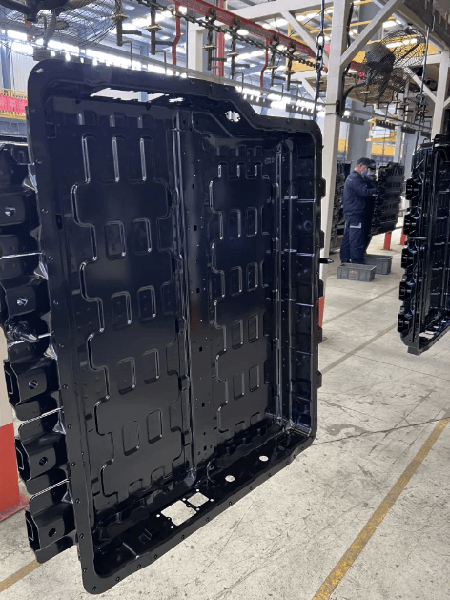
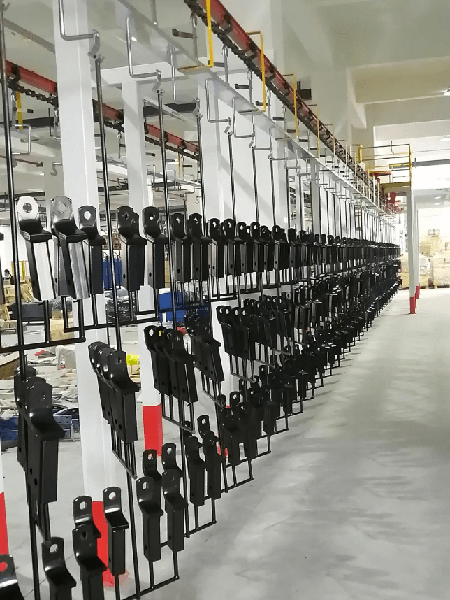
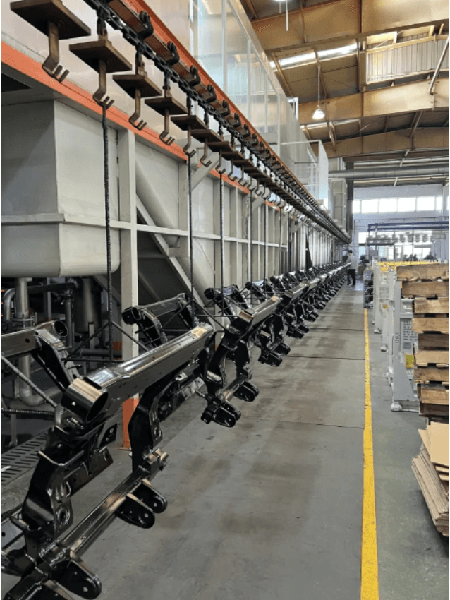
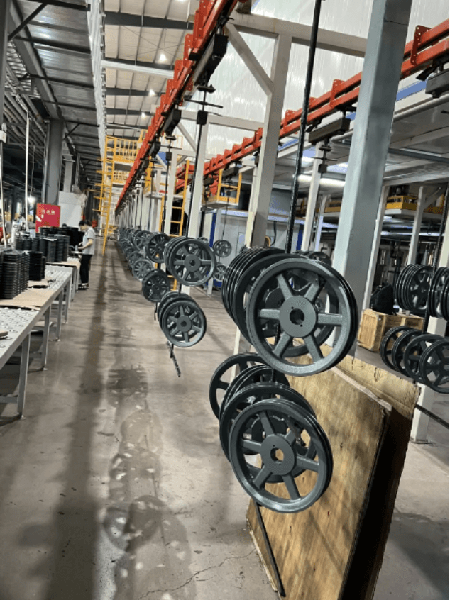
Post time: Jul-25-2025